AI revolutionizes manufacturing through multiple critical applications. Predictive maintenance systems anticipate equipment failures before they happen, while computer vision detects microscopic defects humans miss. Supply chain algorithms optimize inventory levels—no more costly stockouts! AI also enhances workflow efficiency, adjusts production parameters in real-time, and minimizes waste across assembly lines. These technologies aren’t just fancy add-ons; they’re essential competitive tools slashing downtime and boosting quality. Discover how these smart systems are transforming factory floors from reactive to proactive environments.
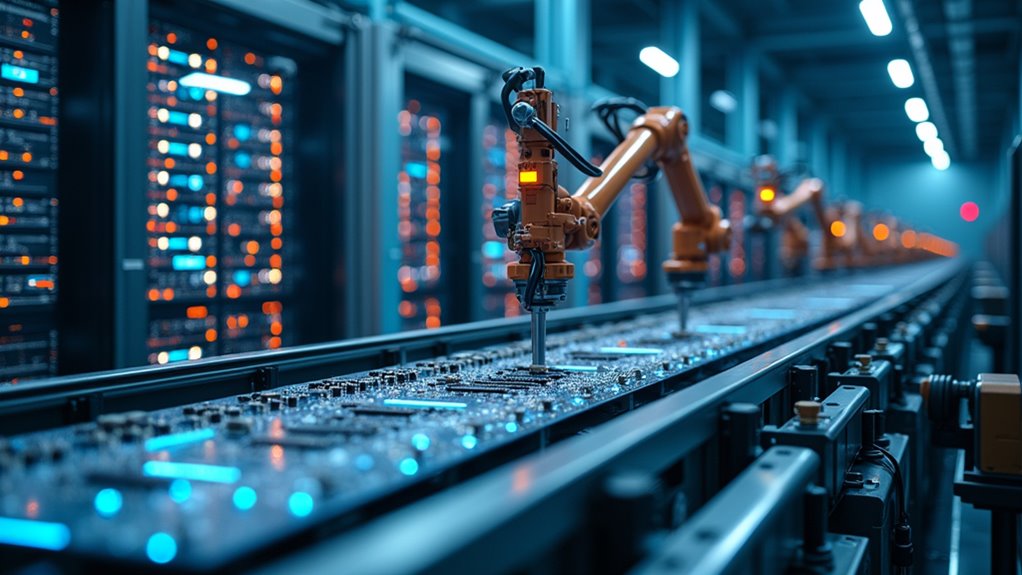
While the manufacturing sector has always sought efficiency, artificial intelligence is revolutionizing the industry in ways previously unimaginable. The integration of AI-powered predictive maintenance systems has transformed how manufacturers approach equipment longevity and operational continuity. These systems analyze vast amounts of equipment data to anticipate potential failures before they occur—yes, they actually predict the future of your machinery.
Smart factories now leverage robotic automation alongside AI analysis to minimize costly downtime that once plagued production lines. Gone are the days of reactive maintenance; modern manufacturers must adopt predictive approaches or risk falling behind.
Embrace AI or watch competitors surge ahead while you fix yesterday’s problems with today’s resources.
AI’s impact extends deeply into supply chain management, where algorithms crunch historical data to forecast demand with remarkable precision. This isn’t your grandfather’s inventory system! Through sophisticated analysis, AI optimizes inventory levels to prevent both costly overstocking and reputation-damaging stockouts. Major retailers like Walmart uses AI for inventory optimization and demand forecasting to maintain competitive advantage.
Logistics operations benefit from routing algorithms that determine the fastest, most economical delivery paths—saving time, fuel, and customer patience. Real-time data from IoT devices enables AI systems to make intelligent decisions that enhance overall operational efficiency.
Quality control has been revolutionized through AI-driven computer vision systems that detect microscopic defects invisible to human inspectors. These systems tirelessly monitor production in real-time, guaranteeing consistent quality while dramatically reducing the time needed to identify and resolve issues. The result? Higher quality products, fewer returns, and happier customers.
On assembly lines, AI continuously analyzes and optimizes workflows to reduce downtime and improve efficiency. It integrates with predictive maintenance schedules to guarantee operations run smoothly while adapting production parameters to meet changing demand patterns.
This flexibility minimizes waste and maximizes resource utilization—something every manufacturer cares deeply about. AI’s pattern recognition capabilities identify equipment trends that might indicate future problems, enabling truly data-driven decisions that impact the bottom line. Similar to healthcare applications, manufacturing AI systems use predictive analytics to detect potential issues before they escalate into costly problems.
Through real-time monitoring and analysis, manufacturers can immediately adjust operations to maintain peak performance. In today’s competitive manufacturing landscape, those who embrace AI technologies gain significant advantages in efficiency, quality, and cost-effectiveness.
Frequently Asked Questions
What Skills Do Workers Need to Adapt to AI Manufacturing?
Manufacturing workers need AI training to thrive in smart factories. Workforce adaptability isn’t optional—it’s survival.
Technical skills with machines and data analysis capabilities separate the employable from the obsolete. Workers must embrace problem solving with AI systems, not fear them.
Continuous learning becomes part of the job description, not an extra. The factory floor demands humans who can interpret AI insights, troubleshoot systems, and pivot when technology evolves.
How Expensive Is Implementing AI in Small Manufacturing Businesses?
Implementing AI in small manufacturing isn’t cheap. Initial investments typically range from $5,000 to $30,000—a significant hurdle for businesses with tight budget constraints.
A proper cost analysis reveals ongoing expenses too: cloud services, maintenance, and system upgrades.
The good news? Off-the-shelf AI solutions offer more affordable entry points than custom development.
Yes, upfront costs sting, but many manufacturers find the efficiency gains worth it within 2-5 years.
Choose wisely or your wallet will notice!
Can AI Manufacturing Systems Be Retrofitted to Existing Machinery?
Yes, existing machinery can absolutely be retrofitted with AI systems.
Retrofitting machinery offers a cost-effective alternative to complete replacement, though AI integration challenges exist. Sensors, IoT devices, and communication protocols are the backbone of these upgrades.
The process requires addressing system compatibility issues and often demands staff training. Despite these hurdles, the payoff is substantial—extended equipment life, reduced downtime, and improved production efficiency make retrofitting an increasingly popular choice for manufacturers looking to modernize without breaking the bank.
What Cybersecurity Risks Come With AI Manufacturing Integration?
AI manufacturing integration introduces significant cybersecurity risks.
External connections to cloud-hosted AI models create vulnerabilities for attackers to exploit.
AI vulnerabilities include complex, opaque decision-making processes that complicate monitoring.
Robust cybersecurity protocols must include multi-factor authentication and limited remote access.
Data privacy concerns escalate as AI systems handle sensitive production information.
Effective risk management requires regular security assessments and staff training.
How Does AI Manufacturing Impact Environmental Sustainability Goals?
AI efficiency revolutionizes environmental sustainability goals in manufacturing. It optimizes energy consumption, slashing those pesky carbon emissions while maintaining productivity.
Smart algorithms predict maintenance needs, reducing unnecessary waste and downtime. The technology transforms resource management by analyzing usage patterns—hello, less material waste!
Sustainable practices become achievable through AI-driven supply chain optimization and precise demand forecasting. Companies can finally track their carbon footprint accurately, making environmental compliance less of a headache and more of a competitive advantage.